تست های آزمایشگاهی شامل موارد مختلفی است که از قبیل:
- آزمون سختی سنجی
- آزمون کشش
- آزمون مقاومت سایشی
- آزمون چسبندگی به سطح فلز
در ادامه به تفصیل توضیحات هر مورد ارائه میگردد:
1- آزمون سختی سنجی
سختی بیانگر مقاومت در برابر فرورفتگی توسط یک جسم سخت تر میباشد. در آزمایشگاه صنایع لاستیکی پادسپاهان این تست بر اساس استاندارد ASTM D 2240 و به کمک سختی سنج SHORE A و SHORE D برای تعیین سختی لاستیک قطعات، روکش غلتک و رابر لاینینگ و … انجام میگیرد.
سختی سنج SHORE A برای مواد نسبتا نرم مثل لاستیک پخت شده (سوزن به شکل مخروط ناقص) و سختی سنج SHORE D برای مواد سخت مثل ابونیت (سوزن به شکل مخروط با نوک کروی) استفاده میگردد.
سختی با مقدار نفوذ سوزن رابطه عکس داشته و وابسته به مدول الاستیک و رفتار ویسکوز الاستیک ماده است و پس از زمان 1±0.1 s خوانده میشود و به دو روش دستی و غیر دستی (توسط پایه) انجام میگیرد.
با توجه به اینکه میزان فشار وارده بر میزان سختی تاثیرگذار است لذا جهت مقایسه داده های سختی نمونه، بایستی از پایه استفاده گردد. برای سختی SHORE A وزن 1kg و برای سختی SHORE D وزن 5kg اعمال میشود.
شرایط انجام آزمون و گزارش دهی
1- ضخامت نمونه بایستی حداقل 6 میلیمتر باشد.
2- دو طرف سطح نمونه بایستی صاف و موازی با یکدیگر باشد.
3- نمونه باید حداقل 12ساعت در محیط استاندارد آزمایشگاه قر ارگیرد.
4- سختی در 5 نقطه مختلف با فواصل 6 میلیمتر از یکدیگر و 12 میلیمتر از لبه گرفته میشود و بصورت میانگین حسابی یا داده وسط گزارش میگردد.
5- سختی به شکل M/60/1 گزارش میگردد. که در آن M: نوع سختی سنج، 60: مقدار سختی، 1: زمان (ثانیه) پایه در تماس با نمونه است.
2- آزمون کشش
استحکام کششی بیانگر توانایی پلیمر در برابر حداکثر تنش اعمالی و تغییر شکل از حالت الاستیک به پلاستیک میباشد.
آزمون کشش در آزمایشگاه صنایع لاستیکی پاد سپاهان بر اساس استاندارد ASTM D412 (روش A یعنی نمونه دمبلی شکل و بر اساس قالب نوع C ) توسط نرم افزار تنسایل جهت اندازه گیری خواص کششی ، مدول ، بیشینه نیروی کششی و ازدیاد طول تا نقطه پارگی کلاستیک پخت شده و تر موپلاستیک الاستو مرها جهت تولید قطعات، روکش غلتک، رابر لاینینگ و …. انجام میگیرد . (این آزمون مناسب نمونه های ابونیت و باسختی مشابه ابونیت نمیباشد)
شرایط انجام آزمون و گزارش دهی
1- برای مقایسه نتایج نمونه های مختلف بایستی شرایط آزمونشان ( سرعت کشش، دما، رطوبت، هندسه نمونه، شرایط محیطی قبل از آزمون و …) کامل یکسان باشد.
2- تهیه شیت طبق استاندارد ASTM D3182 (ضخامت نمونه بین 1.3 تا 3.3 میلیمتر )
3- نمونه باید حد اقل 3 ساعت در شر ایط استاندارد آزمایشگاه قرار گیرد .
4- تهیه دمبل از شیت توسط قالب نوع C
5-اندازه گیری عر ض و ضخامت نمونه دمبل (اند ازه گیر ی سه قسمت میانی و د وطرف و ثبت بصورت میانگین اندازه ها)
6- اگر تفاوت بین بیشترین و کمترین ضخامت قسمت های مختلف نمونه بیش از 0.08 میلیمتر باشد نمونه مردود است.
7- آزمون بر روی حد اقل 3 نمونه باید انجام و نتیجه بصو رت میانگین گزارش میگردد . (در صورت اختلاف زیاد بین د اده ها آزمون تا 5 نمونه انجام و نتیجه بصورت میانه گزارش میشود )
محاسبات
- تنش کششی برابر است با نیرو تقسیم بر سطح مقطع نمونه
- ازدیاد طول یا کرنش برابر است با تغییرات طول تقسیم بر طول اولیه بصورت درصد
- مدول برابر است با تنش تقسیم بر کرنش
نمونه ای از نمودار خروجی از نرم افزار که محور Y میتواند تنش یا نیرو باشد و محور X میتواند کرنش، طول یا زمان باشد:
نمونه ای از پارامترها و داده های خروجی از نرم افزار:
قالب پانچ دمبل کشش به همراه نمونه دمبل:
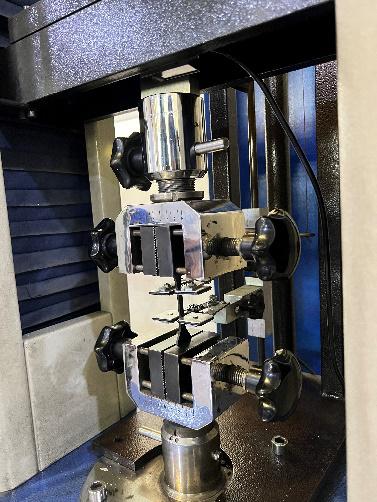
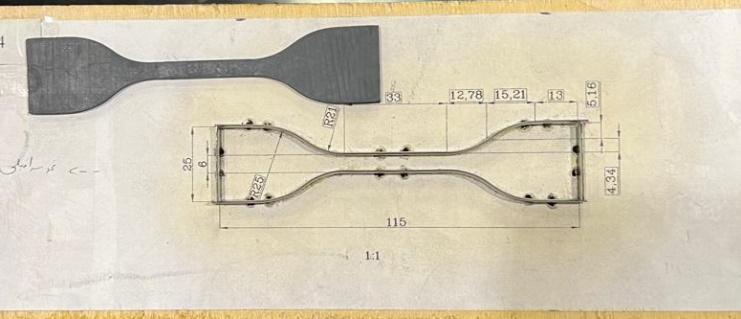
3. آزمون مقاومت سایشی با استفاده از غلتک استوانه ای چرخان
مقاومت سایش بیانگر مقاومت در برابر فرسودگی تدریجی است. آزمون مقاومت سایشی در آزمایشگاه صنایع لاستیکی پادسپاهان بر اساس استاندارد ISO 4649 به هر دو روش A و B (نمونه بدون چرخش و در حال چرخش) جهت اندازه گیری مقاومت سایشی (مقدار حجم از دست رفته نمونه آزمون بعد از سایش بوسیله صفحه سمباده بر حسب میلیمتر مکعب) و شاخص مقاومت سایشی (نسبت حجم از دست رفته کامپاند مرجع به حجم از دست رفته نمونه آزمون برحسب درصد) برروی لاستیک پخت شده و ترموپلاستیک ها جهت تولید قطعات، روکش غلتک، رابر لاینینگ و …. انجام میگیرد.
شرایط آزمون و گزارش دهی نتایج
1- نمونه باید استوانه ای شکل با قطر 16±0.2 میلیمتر با حداقل ارتفاع 6 mm باشد.
2- حداقل زمان بین پخت نمونه و آزمون 16 ساعت و حداکثر آن 4 هفته باشد.
3- مقدار بیرون آمده قرص از لبه قسمت فلزی نگهدارنده 2±0.2میلیمتر باشد.
4- در صورت کاهش وزن نمونه بیش از 400 میلی گرم نمونه به جای مسافت 40 متر معمولا در مسافت 20 متر آزمون انجام میشود.
5- صفحه سمباده توسط کامپاند مرجع کالیبره می گردد. (اگر کاهش وزن نمونه مرجع بین 180 تا 220 میلی گرم باشد میزان زبری سمباده استاندارد است در غیر اینصورت باید سمباده اصلاح یا تعویض گردد)
6- وزن اولیه نمونه توسط ترازو اندازه گیری میشود، وزن ثانویه نمونه پس از سایش بر روی سنباده نیز توسط ترازو اندازه گیری میشود و دانسیته نمونه طبق استاندارد 2781 ISO اندازه گیری میشود .
7- میانگین سه نمونه به عنوان جواب آزمون گزارش میگردد.
محاسبات
حجم نسبی از دست رفته(Relative volume):
Relative volume:
: جرم از دست رفته نمونه آزمون (mg) و : چگالی نمونه آزمون (mg/mm3)
: مقدار ثابت جرم از دست رفته کامپاند مرجع (بر حسب mg) برای کامپاند مرجع شماره 1 و روش آزمون B : مقدار 250 mg و برای کامپاند مرجع شماره 1 و روش آزمون A: مقدار 200 mg تعریف شده است.
: جرم از دست رفته کامپاند مرجع (mg)
شاخص مقاومت سایشی:
Abrasion resistance index:
: جرم از دست رفته نمونه آزمون (mg) و : دانسیته نمونه آزمون (mg/mm3)
: جرم از دست رفته کامپاند مرجع (mg) و : دانسیته کامپاند مرجع(mg/mm3)
4.آزمون چسبندگی به سطح فلز
آزمون چسبندگی به سطح فلز بیانگر میزان مقاومت چسبندگی استاتیک لاستیک به زیرآیند سخت مانند فلز میباشد.
این آزمون در آزمایشگاه صنایع لاستیکی پاد سپاهان بر اساس استاندارد ASTM D429 مطابق روش B (زاویه 90 درجه) جهت تست میزان چسبندگی لاستیک به فلز در قطعات فلز دار مانند غلتک، گیت، رابرلاینینگ و … انجام میگیرد.
شرایط آزمون و گزارش دهی نتایج
1- نمونه دارای عرض 25±0.5mm ، ضخامت 6.3±0.1mm و طول 125mm می باشد.
2- ضخامت فلز 1.6±0.1mm با عرض 25±0.5mm و طول 60±1mm می باشد.
3- ابتدا فلزهای لازم جهت آزمون را سند بلاست نمو ده. قبل از هر گونه آلودگی سطح فلز، سطح فلز را کاملا با پرایمر آغشته و پس از خشک شدن سطح، حداقل یک ساعت، یک ناحیه با ابعاد مربعی 25mm*25mm تقریبا وسط فلز جدا نموده و بقیه را با یک لایه چسب نواری پوشانده تا مانع از چسبیدن لاستیک به فلز گردد. قسمت میانی را به چسب آغشته کنید و حداقل یک ساعت صبر کنید تا خشک شود. ضخامت لاستیک نیز حدود 8mmمیباشد.
4- پس از فرآیند پخت، نمونه بایستی در دمای استاندارد2ºC 23± برای مدت زمان 16 ساعت نگه داشته و سپس آزمون انجام شود.
5- آزمون توسط دستگاه تنسایل با سرعت جدایش فک ها 50±5 mm/min انجام میشود.
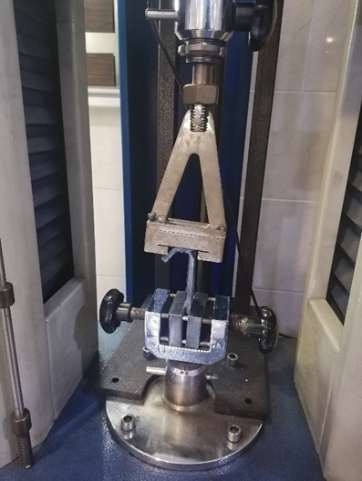
6- پس از بستن فک چسبند دگی و قراردادن نمونه در پایان تست سطح جدا شده لاستیک و سطح فلز را بررسی و نوع جدایش را بر اساس درصد به شرح زیر گزارش میگردد.
R: جدایش لاستیک از لاستیک ، RC: جدایش از فصل مشترک لاستیک و چسب
CP: جدایش از فصل مشترک پرایمر و چسب ، M(CM): جدایش از فصل مشترک فلز و پرایمر
مثال: RC-50,M-50 ، یعنی 50 درصد جدایی ها از فصل مشترک فلز و پرایمر بوده و 50 درصد نیز از فصل مشترک لاستیک و چسب بوده است. مقدار چسبندگی نیز با واحد N/mm گزارش میگردد (داده نرم افزار ).